In recent years, there have been several trends and technologies in metal fabrication that have emerged to change the face of this industry. These include automation and robotics, 3D printing, computer-aided design and manufacturing, additive manufacturing, advanced materials, and the integration of IoT and Industry 4.0 technologies. These developments have led to increased efficiency, precision, cost-effectiveness, and the ability to create complex and unique designs in metal fabrication. As these trends continue to evolve and improve in the next 202x (with an outlook for the next 8 years), we can expect to see even greater advancements in the metal fabrication industry in the future.
1. Automation and Collaborative Robotics
The metal fabrication industry has been utilizing robotics for quite some time, mainly for tasks that are deemed too dangerous for human workers. However, traditional robots were large in size and required dedicated working spaces.
With the advancements in robotics technology, collaborative robots or cobots have emerged, which can work alongside human workers to complete tasks safely. These cobots are particularly useful for dangerous or repetitive tasks, and are increasingly being used to address the labour shortage in the industry, which has been further exacerbated by the COVID-19 pandemic.
Although cobots are still relatively new technology in the metal fabrication industry, they are quickly proving to be a valuable asset. Soon, it is confirmed that automation is being increasingly used in metal fabrication to improve efficiency, reduce costs, and increase precision. Robots are being used to perform tasks such as welding, cutting, and drilling.
2. 3D Printing and Additive Manufacturing:
3D printing, once considered a tool for hobbyists, has quickly become a valuable tool across various industries, including metal fabrication. Additive manufacturing, also known as 3D printing, provides unparalleled levels of customization in the metal fabrication industry.
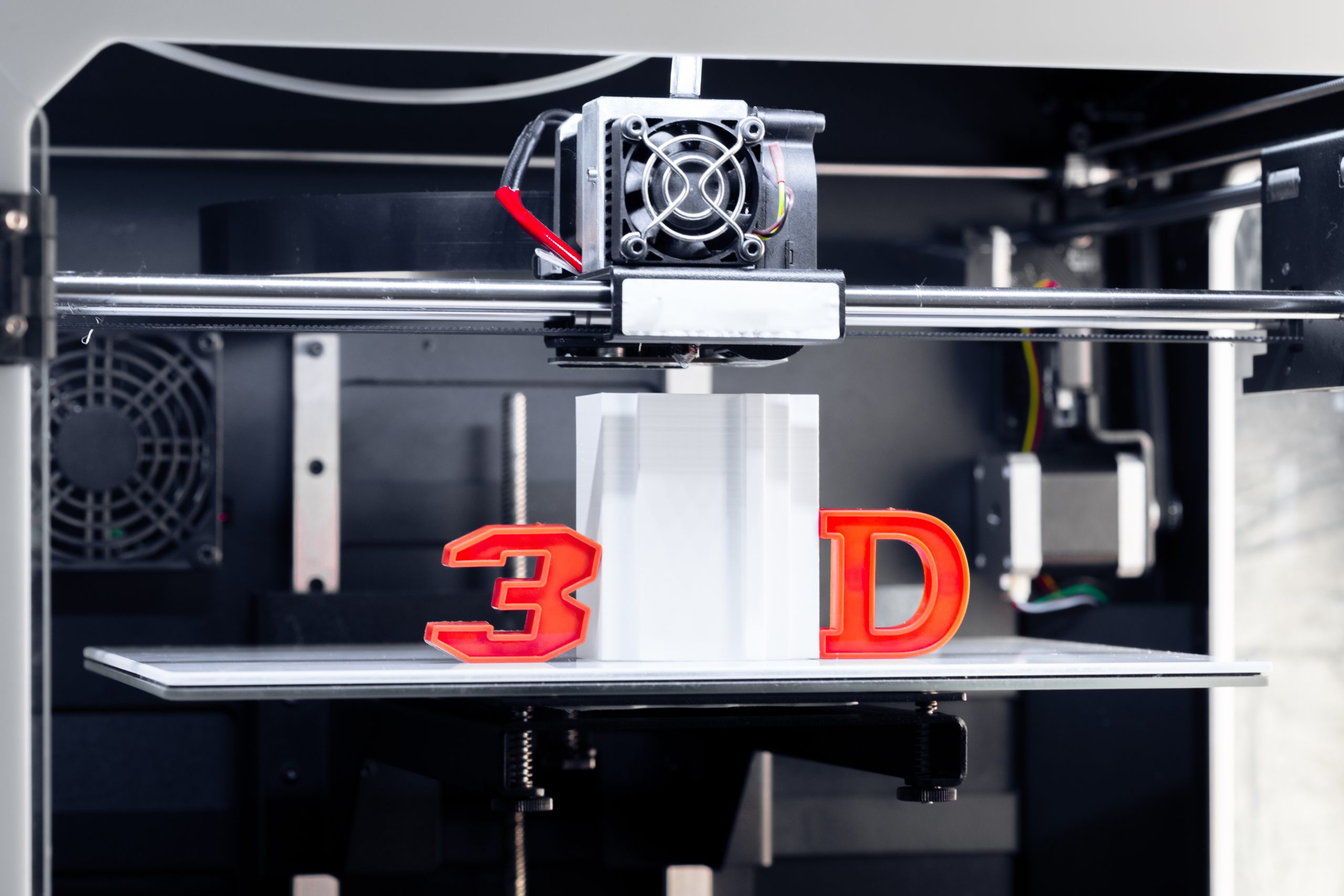
3D printing is being used to create metal parts, casting molds and prototypes quickly and cost-effectively. This technology allows for the creation of complex geometries and shapes that would be difficult to produce using traditional manufacturing methods. One specific method, Metal powder bed fusion, enables manufacturers to create complex designs with minimal waste, as any unused powder can be recycled and reused. This technology is revolutionizing the way metal fabrication is done and providing new opportunities for innovation.
3. Implementing Automation and CNC Machines
Computer numerical control (CNC) machines are an integral part of the metal fabrication industry, but until recently, they required human intervention and programming to function. Incorporating automation into the CNC portion of metal fabrication can remove some repetitiveness from this step, increasing efficiency and productivity in the long run.
Eliminating repetition reduces the chance of employees developing repetitive stress injuries, which also opens them up for better opportunities in their careers. CNC automation is becoming more popular during 2020 and will continue to thrive as the industry moves into the future.
4. Internet of things (IoT) and Industry 4.0
The Internet of Things (IoT) is becoming an increasingly important aspect of metal fabrication equipment control. IoT devices and sensors can be integrated into metal fabrication equipment to provide real-time data and monitoring of the equipment’s performance and usage. This data can then be analyzed to optimize equipment operation and maintenance, leading to increased efficiency and cost savings.
Additionally, IoT-enabled equipment can be remotely monitored and controlled, allowing for greater flexibility and improved collaboration between different teams and facilities. The integration of IoT technology also enables Predictive maintenance, by using data from the machines and sensors to predict when maintenance is needed, reducing downtime, and increasing the life of the machines.
5. Computer-Aided Design (CAD) and Computer-Aided Manufacturing (CAM)
The use of Computer-Aided Design (CAD) and Computer-Aided Manufacturing (CAM) software in metal fabrication is becoming increasingly popular as it allows for greater precision and efficiency in the design and manufacturing process. CAD software allows designers and engineers to create detailed, accurate 3D models of the parts or products they want to fabricate. These models can then be simulated and tested before actual fabrication begins, reducing the risk of errors and wasted materials.
CAM software, on the other hand, allows for the efficient programming of CNC machines to perform the fabrication process according to the specifications of the CAD model. This can lead to increased accuracy and consistency in the final product, and reduced lead time and costs. Additionally, these software can be integrated with other digital technologies such as IoT and simulation software, to enhance the overall efficiency and automation of the fabrication process.
6. Embracing Digitisation
Despite the ongoing digital revolution in many industries, it has been relatively slow to adopt new technologies in metal fabrication. However, it’s important to note that implementing technology-based platforms doesn’t mean replacing human workers.
Rather, it’s a step towards increased efficiency and productivity. As business owners in the metal fabrication industry, it is crucial to embrace digitization and leverage the tools available to them. This includes not only the use of digitized technology but also the need for cybersecurity measures to protect against potential threats. While the adoption of new technologies in metal fabrication may come with some challenges, the benefits it brings to the industry are well worth the effort.
7. Advanced materials
- Advanced materials allow for greater strength, durability, and versatility in the final product. These materials include, but not limited to:
- High-strength steels: These steels have a higher yield strength and tensile strength compared to traditional steels, allowing for thinner and lighter parts to be produced while maintaining the same level of strength and durability.
- Aluminum alloys: These alloys have a lower density than steels, making them ideal for lightweight applications such as aerospace and automotive parts. They also have good corrosion resistance and high thermal conductivity.
- Titanium alloys: These alloys have an excellent strength-to-weight ratio and high corrosion resistance, making them ideal for aerospace and medical applications.
- Copper alloys: Copper alloys have good electrical conductivity, thermal conductivity, and corrosion resistance, making them ideal for electrical and electronic applications.
- Composites: Composites are made of a combination of different materials such as fibers, ceramics, and metals. These materials have unique properties that can be tailored to specific applications, such as high strength, low weight, and corrosion resistance.
Using these advanced materials in metal fabrication allows manufacturers to produce parts and products with improved properties, such as increased strength and lightness, as well as improved resistance to corrosion and heat. This can lead to increased performance and efficiency in various industries and applications, such as aerospace, automotive, medical, and energy.
Changes in Metal Fabrication Beyond 2023
We’re in the early stage of a new decade, the trends and technologies in metal fabrication we’ve seen since 2020 will continue to grow and adapt as we make our way into the future. Things like digitalisation, collaborative robots and 3D printing will continue making the metal fabrication industry more efficient and productive as we look at 2023 and beyond.
As a professional metal fabricator, AM Industries Vietnam constantly put our effort to improve our manufacturing capacity toward new automation technology and softwares. Please feel free to contact us via sales@aminds.com if you have any question or need futher information.
Our Services – Select the one you would like to know more about